Since its inception in 1953, Bucher has been providing world-leading innovative interior aircraft solutions for the aviation and air rescue sectors.
In Fällanden, Switzerland, founder Heinrich Bucher laid the groundwork for a business that now also operates from bases in Sinn-Fleisbach, Germany, and Everett, USA.
Counting original equipment manufacturers (OEMs) such as Airbus and Boeing among their customers, Bucher has become a trusted partner in providing interior aircraft solutions including Galleys, Stowages, Front Row Monuments, Crew Workstations, Branding- and Design Elements, Partitions, Doghouses, SkyBassinets, Class Dividers and Self-Service Counters.
In a recent interview with AeroTime, Group CEO Beat Burlet and Director of Engineering David Keller provided some fascinating insights into the world of interior aircraft solutions, how the company handles global supply challenges and why they are always in search of the next generation of lightweight materials.
According to Beat Burlet, Bucher offers its customers “ingenious solutions, reliable products and first-class service”, and strives to “reach new heights in lightweight construction for both aviation and air rescue”.
As well as aerospace giants Airbus and Boeing, Bucher includes leading airlines such as Lufthansa, SWISS, Condor., JetBlue, Air Greenland, Virgin Atlantic and Cebu Pacific among its customer partners.
“We serve OEMs as well as airline customers,” Beat Burlet told AeroTime. “The requirements are different but there are also some characteristics which are the same for both customer groups, and that is quality and reliability. However, in terms of design, in terms of manufacturing processes, the customers have slightly different requirements.”
Most recently, Bucher installed interior monuments, branding elements and stowage with self-service counter for business class passengers on Malaysia Airlines’ fleet of new Airbus A330-900s.
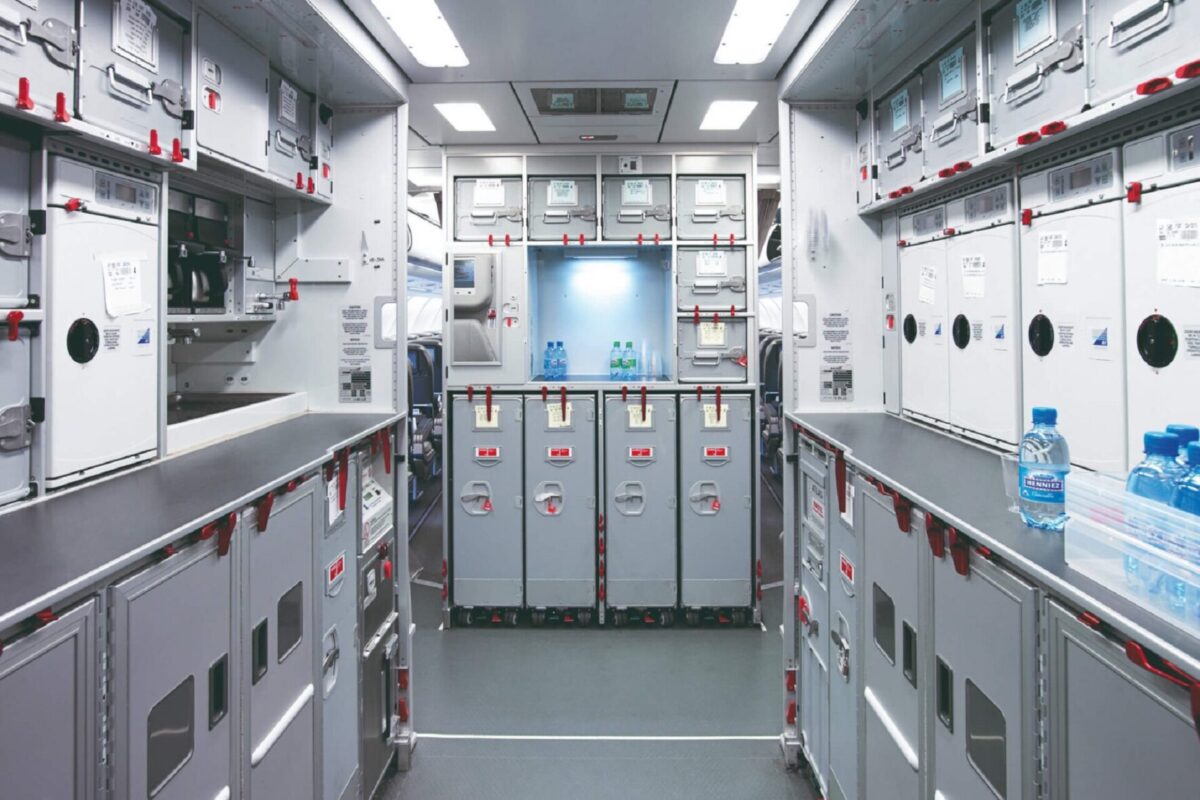
Designing products for aircraft to fly with “minimum weight and maximum reliability” has been the central vision of Bucher’s success and continues to shape the company’s future.
“One of the main drivers we see is reducing weight, and this is what drives our manufacturing technologies and the materials we use. So, we see a trend towards lighter materials. Of course, we also see on the other hand a trend towards using less carbon footprint materials in production and end of life,” David Keller told AeroTime.
The COVID-19 pandemic left many airlines nervous about investing in the future, but now with a resurgence in aircraft orders from Boeing and Airbus, demand for Bucher’s expertise should also increase.
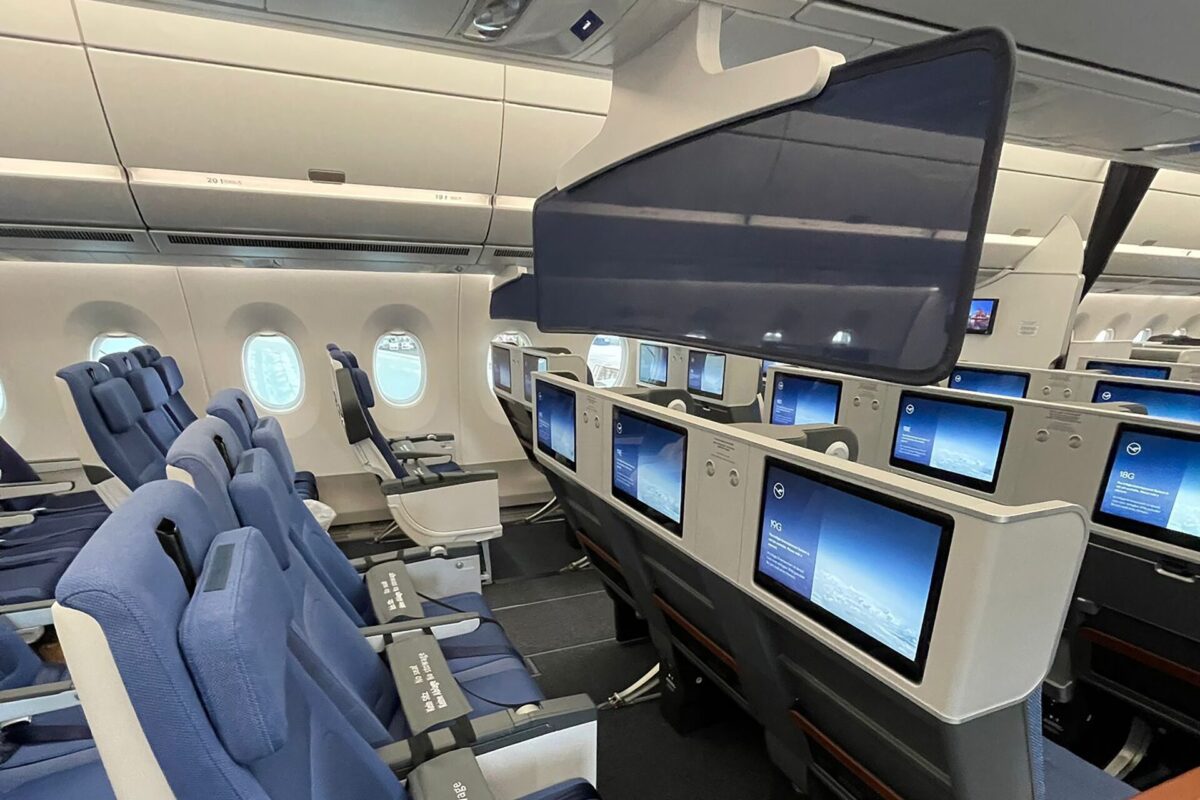
According to Bucher, OEMs such as Airbus and Boeing are expected to produce around 40,000 aircraft over the next 20 years, so demand for its galleys is set to hit record levels.
“These are production rates that we haven’t seen even before Coronavirus, and those numbers, plus what’s going on in the retrofit market, clearly equals a higher demand of galleys than what we’ve seen so far,” Beat Burlet said.
Bucher prides itself on its products that which are designed to last for the entire lifetime of the aircraft on which they are installed.
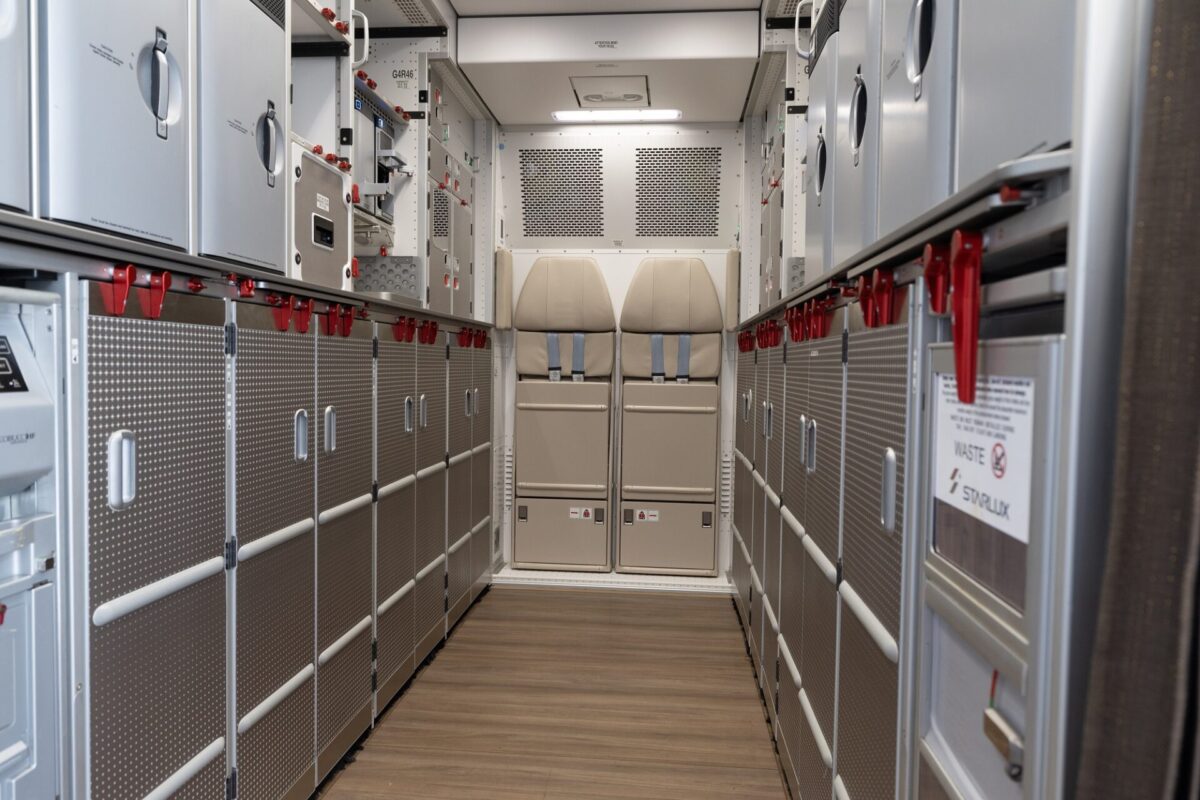
“We put our emphasis on quality and reliability of our products. We designed the galleys to last as long as the aircraft airframe,” Burlet explained.
Recently, an aircraft with a galley installed by Bucher 17 years ago returned to the company for an overhaul and Keller noted that the installation remained in excellent condition despite four different airlines operating the plane.
“It’s really interesting, because we don’t often have the chance to see what happens with our product after the first delivery, but here we have the whole story,” David Keller said.
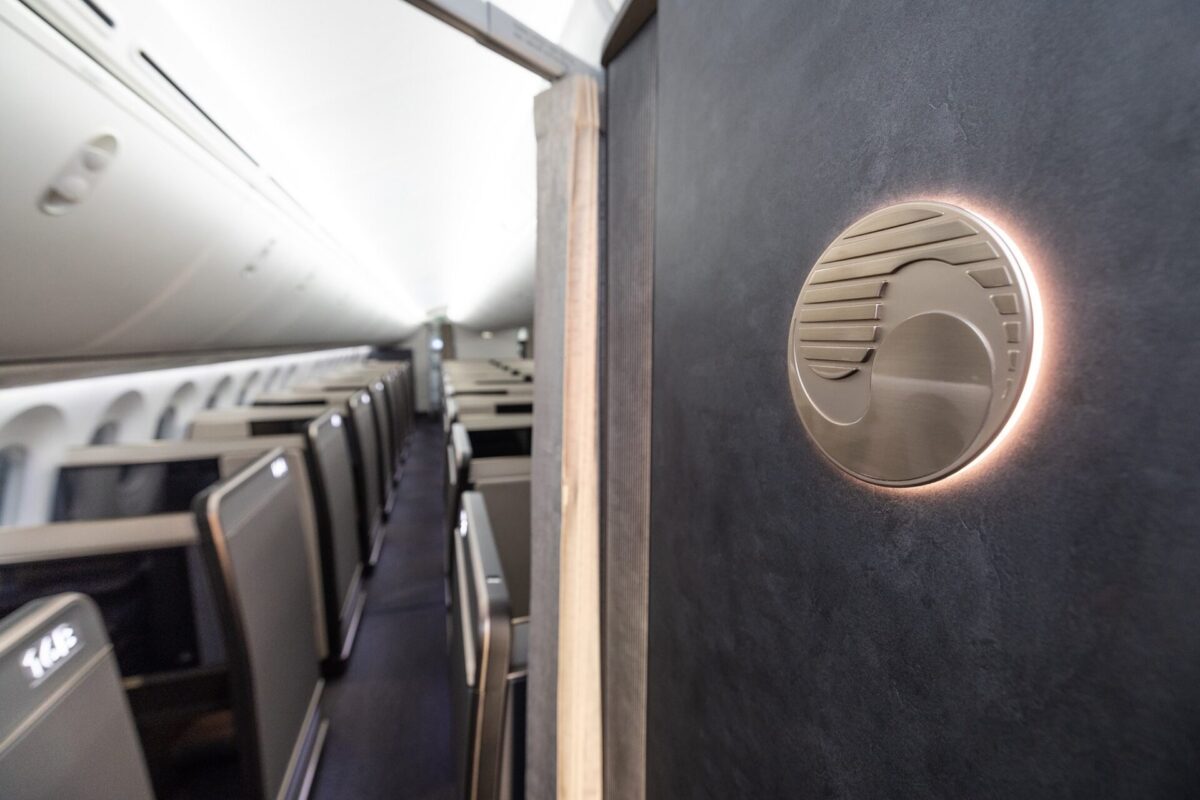
As well as planes, Bucher also provides interior solutions to the train industry, but it is perhaps of particular note the work the company has done within the helicopter sector.
While working in partnership with law enforcement, military, and multi-mission operators, Bucher also provides solutions for helicopters working within emergency medical services installing life-saving equipment to help people when they are most in need.
“With a focus on quality and safety, our solutions are designed to withstand the rigors of intense missions and offer a range of features that ensure reliable and dependable performance,” Bucher said.