After years spent developing countless renderings, concept experimentation and tests, the electric vertical takeoff and landing (eVTOL) aircraft industry appears poised to finally make its public debut.
But which country will be the first to launch an eVTOL into service remains to be seen. Will it be the Middle East, where Dubai, Abu Dhabi and Saudi Arabia have rolled out the red carpet for eVTOL developers? Or a mass event, such as the 2025 World Expo in Osaka, which boasts a dense advanced air mobility program?
There are a handful of eVTOL developers which are already ahead of the pack, at least when it comes to the stage of technological development. The likes of Joby Aviation, Archer Aviation, BETA Technologies, Lilium, Volocopter and Vertical Aerospace, are edging increasingly closer to certification and (provided they manage to secure a long-enough financial runway) entry into service. In the case of Chinese firms such as EHang and AutoFlight, some limited forms of certification have already been granted.
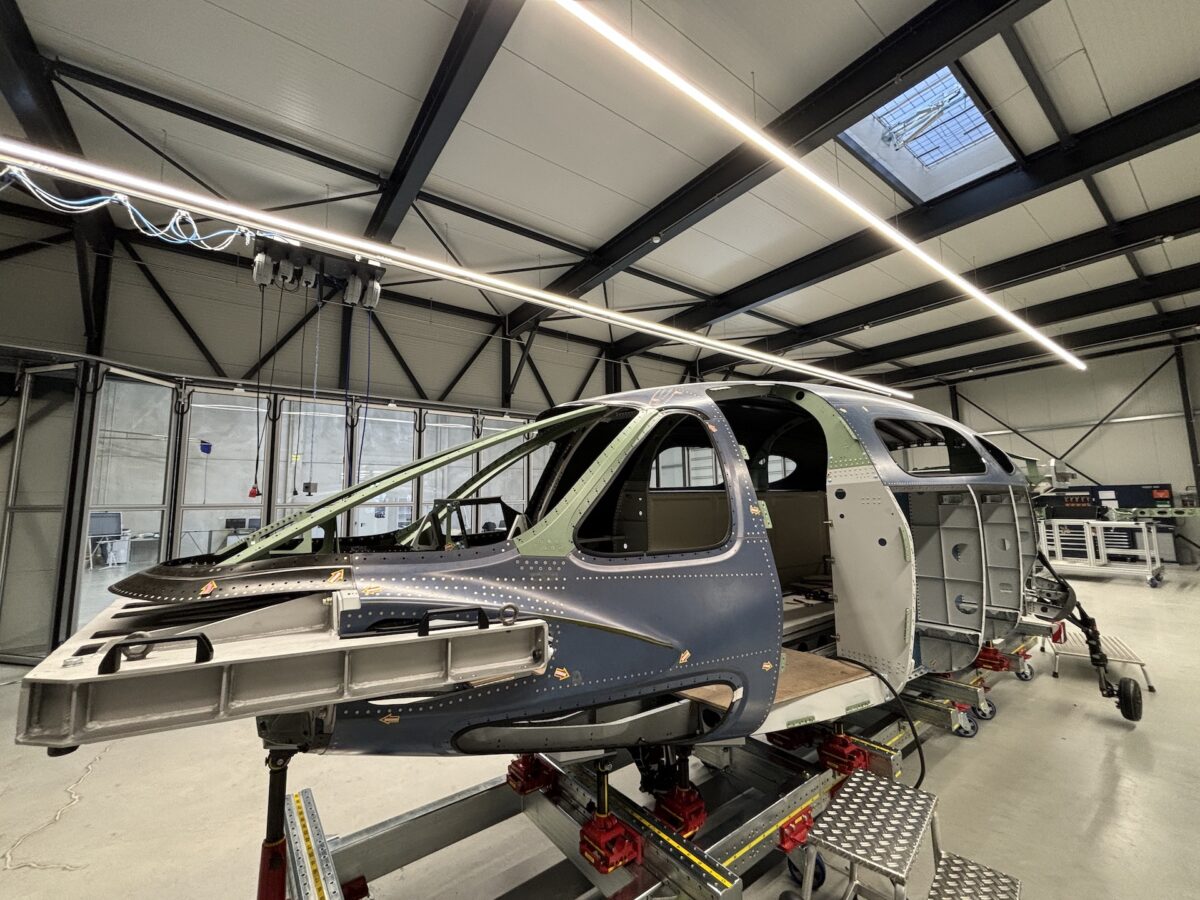
What makes this race particularly interesting is that there does not seem to be a consensus among industry experts regarding the optimal airframe design for an eVTOL.
However, one thing is clear. If any of these aircraft are to fulfil expectations and make money for investors, it will need to be manufactured at scale. But here’s the problem: despite the pioneer energy that pervades this segment of the industry, making airplanes in 2024 is nothing like it was during the time of the Wright Brothers.
From prototype to mass-production
Meeting today’s stringent quality and safety requirements, while also delivering a product that is lightweight, reliable, and cost-effective, will require the adoption of manufacturing and supply management processes.
It’s one thing to build a couple of prototypes, but it is an entirely different matter to churn out aircraft by the thousands, as some developers envisage happening before the end of the decade.
While startups and entrepreneurs have been the initial force behind the emergence of the eVTOL industry, the “traditional” aerospace industry, from the major OEMs to myriad other companies across the supply chain, has also started to take notice. And, interestingly, since one of the hypothetical primary use cases of eVTOLs is urban mobility, so has the automotive industry.
Some of its major players, such as Stellantis, Hyundai and Toyota, have become investors in or partners of leading advanced air mobility companies.
These companies have much to bring to the table, particularly when it comes to managing complex supply chains and mass industrial processes.
However, there are still many lingering questions about the future course of the eVTOL industry. The first of these refers to the uncertainty about which eVTOL designs will emerge as winners, given the broad diversity of constructive choices.
Notwithstanding these different design philosophies, which become evident when looking at the different prototypes, two elements seem to be quite common throughout the industry.
The first is the use of battery-electric propulsion (regardless of some companies, such as Joby and Sirius, which are also experimenting with hydrogen fuel cells), and the other is the generalized adoption of composite aerostructures.
While a whole electric propulsion ecosystem is currently in its infancy, albeit developing fast, the field of aerostructures already includes some well-established players supplying the aerospace industry.
Tier 1 suppliers have been flocking to the emerging eVTOL industry and have become key partners of its main players. The reasons for this interest in an industry that is still small and plagued with development risks are varied. Some suppliers are scouting for new growth opportunities, while others are, quite plainly, hedging their bets and making sure they don’t miss the boat should eVTOL developers deliver on their promise to disrupt.
But perhaps the most interesting aspect of the eVTOL revolution (-in-the-making) is the possibility of developing technologies, skills and expertise that will spill over to other areas of their business and enhance their competitiveness.
“Our work with some of the leading eVTOL developers has provided us with a great opportunity to develop technologies such as thermoplastics, fast curing resin systems or resin transfer molding methods,” Stefan Schamberger, Director Business Development USA, at FACC, an Austrian firm which is a Tier 1 supplier to the aerospace industry, told AeroTime
In addition to having a proven track record of building key components such as wing parts for major aircraft makers, FACC is making composite aerostructures for eVTOL developers such as Archer, Eve Air Mobility and EHang, among others.
“Some of these technologies will almost certainly be used in the next generation of airlines, as well,” Schamberger added, noting that Airbus, through programs such as “Wing of Tomorrow”, has already been looking at some of these composite technologies.
The executive also noted that, in a world that is already suffering from supply chain constraints, some processes will need to be streamlined if the eVTOL industry is to reach the sort of scale that it has based its business case on. This will require the roll out at scale of innovative processes such as the ones FACC is currently working on, for example, reducing the autoclave curing phase of the process from eight to 10 hours to around one hour.
This is a view shared by Russ Brigham, Programme Director eVTOL at GKN Aerospace, a company which is working closely with eVTOL developers such as Lilium, Vertical Aerospace and Hyundai’s advanced air mobility arm, Supernal.
“Our decision to enter the eVTOL market is driven by the evolving technological demands,” Brigham told AeroTime “The technologies required for eVTOLs today are anticipated to be essential for the next generation of single-aisle aircraft and for other [larger] sustainable aircraft. By engaging in the eVTOL segment, we are positioning ourselves to be at the forefront of these technological advancements.”
Outsourcing supply chains…or not?
This is perhaps the reason one of the leading eVTOL developers, Joby Aviation, has opted to make its aerostructures, as well as many other constructive elements, in-house.
“We have consciously taken a highly vertically integrated approach to the design, testing, and manufacturing of our aircraft that we believe has resulted in faster development cycles, a more performant product, and more opportunities for learnings to be discovered and communicated between our various engineering teams,” a source at Joby told AeroTime following a pre-Farnborough International Airshow Q&A event with media on July 17, 2024. “Using the wing as an example, we have designed the form of our battery packs around the wing of the aircraft, and vice versa, resulting in mass savings and improved systems integration.”
Joby is currently producing a limited number of aircraft at its facilities in Marina, California, but is planning to mass produce its aircraft at a new greenfield factory in Dayton, Ohio.
But Joby’s more vertically integrated (and capital intensive) approach is the exception rather than the rule. So far, most of the other leading eVTOL developers have opted to find partners with both experience and scale in the aerospace industry to produce aerostructures and other key components.
Vertical Aerospace is working with GKN Aerospace, and the Lilium Jet aerostructure, for example, is made by Spanish firm Aciturri, a long time Airbus and Boeing supplier.
It’s a similar story in the United States, where BETA Technologies is relying on Albany Engineered Composites (AEC), which produces the aerostructures for the Alia electric short takeoff and landing (eSTOL) aircraft at its factory in Salt Lake City, Utah.
GKN Aerospace’s Brigham highlighted the importance of having an accredited track record in the aerospace supply chain, as well as in managing certification and industrial processes.
However, despite the synergies with “traditional” aerospace and the related spillover effects, some aspects of the production process are specific to the eVTOL space.
“The technical requirement [weight], production ramp up and ultimate rates puts the eVTOL market beyond the norms of aerospace manufacture,” Brigham said. “The aerostructure development process for eVTOLs is significantly different from that of conventional aircraft. While working on large passenger planes can take a development cycle of up to 10 years, eVTOL projects are much more accelerated, with some timelines as short as two years or even 10 months.”
“This rapid pace necessitates a more agile and responsive approach in both technology development and supply chain management,” he concluded.