The natural world has long been one of the great sources of inspiration for creative minds and a catalyst that forced the big thinkers to demand more.
Limited by their human form, it is perhaps no surprise that the extraordinary abilities of animals and insects became a source of fascination for people.
Stories about birds inspiring people to fly date back centuries with the Icarus tale from Greek Mythology among the earliest and best known.
While the era since Icarus’ fabled death for flying to near to the sun may have passed, an obsession with the natural world as a source of inspiration for technological advancement has never waned.
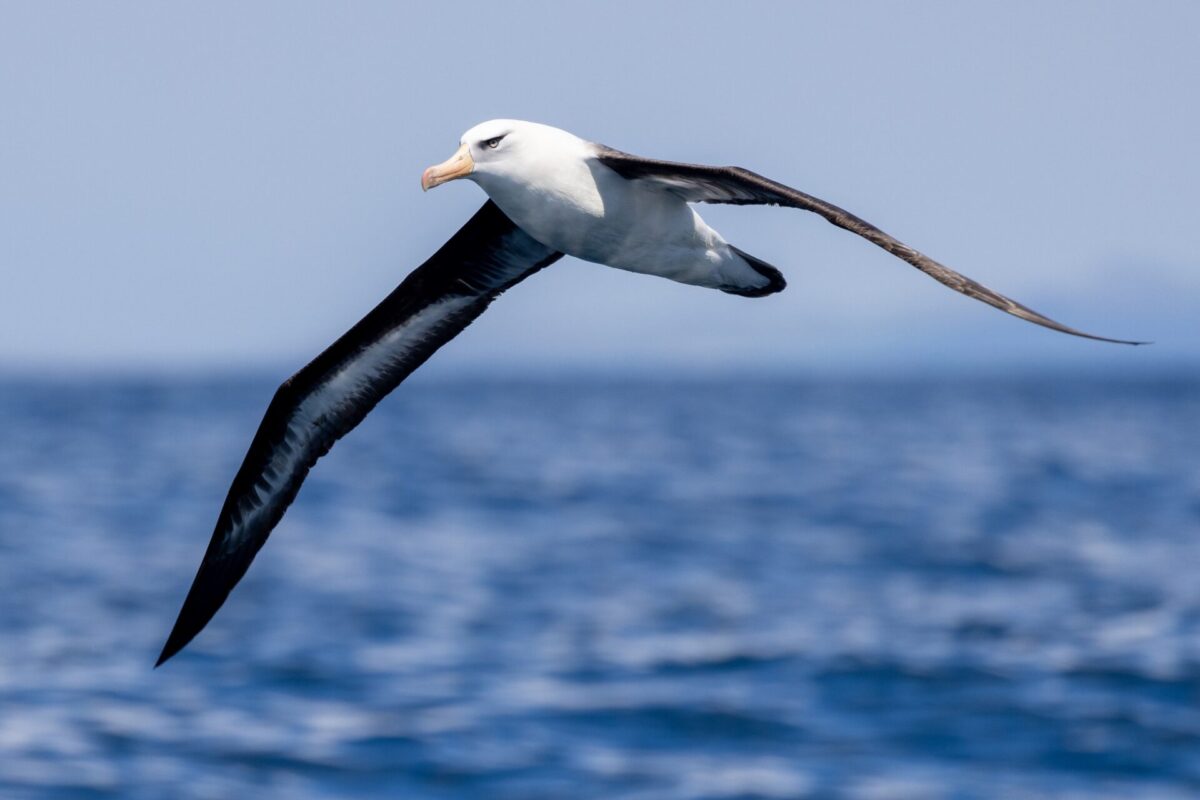
Perhaps unsurprisingly, aviation has made huge strides by investing in biomimicry research and in many respects seen incredible results that have influenced aircraft design and concepts.
AeroSHARK
When Lufthansa Technik announced the development of a durable bionic film that would help save fuel costs, few would have expected the inspiration to have come from the world’s oceans.
But when in October 2024, SWISS became the first to fly a Boeing 777-300ER covered with the new film it was sharks, and specifically their skin, that the airline industry had to thank.
AeroSHARK surface film was developed jointly by Lufthansa Technik and coatings manufacturer BASF and was designed to mimic the microscopic structure of shark skin, optimizing the airflow on an aircraft fuselage and engine nacelles.
Each patch of AeroSHARK film contained millions of 50 micrometers high prism-shaped riblets which enables the aircraft to make significant efficiency gains by reducing fiction on the aircraft.
In December 2023, a Lufthansa Cargo 777F became the first freighter to be modified with AeroSHARK and in December 2023, a LATAM Airlines Brasil Boeing 777 became the first aircraft operated by a carrier in the Americas to be fitted with the film.
This was followed in May 2024, when SWISS announced that it was the first airline to equip an entire fleet of Boeing 777-300ER with the shark skin technology.
Winglets and Sharklets
Both Airbus and Boeing operate aircraft with wingtip devices that are designed to increase aircraft efficiency by removing drag.
According to the Boeing 737 Technical Site, Boeing introduced its first wingtip device in 1988 on Boeing 747-400s, but this was eventually adapted into a blended wingtip which curved upwards rather than at a sharp angle and subsequently became known as Winglets.
However, the first major wingtip device breakthrough came thanks to a NASA-funded project at Langley Research Center during the 1970s.
The person behind the project was an engineer named Richard Whitcombe who found his wingtip inspiration when he noticed that “birds in flight curled their wingtip feathers upward when seeking greater lift”.
The first flight test using Whitcombe’s wingtip device took place on July 24, 1979, at NASA Dryden Flight Research Center and was followed by 47 more.
The devices would prove to “reduce wingtip drag” and increase “fuel efficiency by 6-7%” but would need be positioned uniquely for each aircraft type.
Airbus began delivering its own wing tip device, Sharklets, as an option on newly built A320 family aircraft in December 2012 and offering retrofit options from 2013.
Airbus
Airbus has become a major aviation force behind biomimicry research and in 2020 published a paper setting out some of the ways that aircraft design could be reimagined “by imitating nature’s best-kept secrets”.
fello’fly
The paper included fello’fly which focused on the operational and commercial viability of two aircraft flying together during a long-haul flight in order to reduce fuel consumption.
The idea came from Snow Geese which adopt a ‘V’ formation on extremely long flights to help conserve energy among the group.
“When flying in this way, geese immediately benefit from free lift, which enables them to stay aloft with minimal fatigue over long distances,” said Airbus.
On November 9, 2021, Airbus performed the first long-haul demonstration of formation flight with two A350 aircraft flying at three kilometers apart from Toulouse, France to Montreal, Canada.
Between the French Bee and SAS Scandinavian Airlines A350s more than six tons of CO2 emissions were saved on the trip, confirming the potential for more than a 5% fuel saving on long-haul flights.
AlbatrossONE
In 2019, Airbus announced the AlbatrossONE project which drew its inspiration from one of the world’s largest birds famed for its expansive wingspan and incredible flying technique.
Airbus was drawn to the Albatross’ ability to “lock its wings at the shoulder to fly long distances but unlock its shoulder to better navigate wind speeds”.
A small-scale, remote-controlled aircraft demonstrator featuring “semi-aeroelastic” hinged wingtips was developed and tested by engineers resulting in positive results.
Then in October 2020, Airbus announced that another small-scale demonstrator with wingtips that were 75% longer than those tested in the first phase completed a gate-to-gate flight.
“This latest flight test campaign proves freely flapping wing-tips can alleviate wing loads and avoid tip stall for improved aircraft performance,” Airbus said following the flight.
According to Simple Flying in 2021, AlbatrossONE morphed into the eXtra Performance Wing project and, using another scale model, further flight tunnel testing was conducted.
Under the newly named project Airbus UpNext, a wholly owned subsidiary of Airbus, confirmed a new demonstrator would be used to take the project forward and help develop a wing that can change shape and form during flight to maximize its aerodynamic efficiency.
Join us for the latest development of the eXtra Performance Wing demonstrator ✈️: the removal of the current wings.
— Airbus (@Airbus) November 14, 2024
This demonstrator will test new innovative wings next year that could one day be integrated into future Airbus aircraft to improve fuel efficiency. pic.twitter.com/iD1KzXXI8L
On November 6, 2023, the chosen demonstrator, a modified Cessna Citation VII business jet, flew for the first time and was due to undergo additional flight testing.
Airbus said that a remote operating system would be integrated into the demonstrator, followed by flights to test the communication between the 20 antennas on the aircraft and the control center on the ground.
In a further announcement, Airbus said that the eXtra Performance Wings will be attached to the Cessna and undergo ground testing before the first flights begin in 2025.
Bird of Prey
In 2019 Airbus unveiled a hybrid-electric, turbo-propeller, regional concept aircraft inspired by large birds of prey such as the Bald Eagle.
The bird of prey concept aircraft mimics an eagle’s wing and tail structure and features individually controlled feathers that provide active flight control.
“Although Bird of Prey is not intended to represent an actual aircraft, it does provide insight into what a future regional aircraft could look like based on technologies that currently form the basis of Airbus research. This includes hybrid-electric propulsion, active control systems and advanced composite structures,” said Airbus.
Another bird of prey Airbus has shown an interest in is the Long-eared Owl due to its ability to hunt in almost complete silence.
According to Airbus, the Long-eared Owl is one of only a few birds that has primary feathers serrated like a comb.
While most birds create noise when air flows over the surface of their wings the Long-eared Owl’s serrated feathers muffle the sound by enabling the air to pass easily through.
“Today’s aircraft already produce 75% less noise than those produced 40 years ago. Airbus engineers are studying owls to further unlock the secrets of silent flight. Some ideas include a retractable, brush-like fringe to mimic the owl’s serrated feathers on wings and a velvety coating on aircraft landing gear,” said Airbus.
DragonFly
In January 2023, Airbus UpNext started testing new, on ground and in-flight, pilot assistance technologies on an A350-1000 test aircraft.
Under the DragonFly project the technologies being demonstrated include automated emergency diversion in cruise, automatic landing and taxi assistance.
“These tests are one of several steps in the methodical research of technologies to further enhance operations and improve safety,” said Isabelle Lacaze, Head of Airbus UpNext DragonFly demonstrator, Airbus UpNext. “Inspired by biomimicry, the systems being tested have been designed to identify features in the landscape that enable an aircraft to “see” and safely manoeuver autonomously within its surroundings, in the same way that dragonflies are known to have the ability to recognise landmarks.”
During the flight test campaign, the technologies were able to assist pilots in-flight, managing a simulated incapacitated crew member event, and during landing and taxiing operations.
Taking into account external factors such as flight zones, terrain and weather conditions, the aircraft was able to generate a new flight trajectory plan and communicate with both Air Traffic Control (ATC) and the airline Operations Control Centre.
NASA, Boeing and the Lotus Leaf
In June 2015, NASA and Boeing engineers spent around two weeks testing non-stick wing coatings designed to shed insect residue and help reduce aircraft fuel consumption.
Five different coatings were applied to Boeing’s ecoDemonstrator 757 which conducted 15 flights to put the technology to the test.
The source of inspiration for the coatings came from the Lotus Leaf, which impressed engineers with its ability to disperse water from its surface.
“When you look at a lotus leaf under the microscope the reason water doesn’t stick to it is because it has these rough features that are pointy,” Mia Siochi, a NASA Senior Materials Scientist said. “When liquid sits on the microscopically rough leaf surface, the surface tension keeps it from spreading out, so it rolls off. We’re trying to use that principle in combination with chemistry to prevent bugs from sticking.”
Following conclusion of the research NASA made a patent application for a “Lotus leaf-like nano-textured dust mitigation coating, with hydrophobic properties”.
Morphing wing
In 2016, engineers from NASA and the Massachusetts Institute of Technology (MIT) were working on a new bendable, morphing wing.
The idea meant that an entire airframe could be assembled with a system of tiny, lightweight subunits and the wings covered by a “skin” made of overlapping pieces that resemble scales or feathers.
A test version of the deformable wing designed by MIT and NASA saw the whole shape of the wing being changed and twisted uniformly along its length, by activating two small motors that apply a twisting pressure to each wingtip.
Wind-tunnel tests of this structure type showed that it at least matched the aerodynamic properties of a conventional wing, at about one-tenth the weight.
In 2019, NASA and MIT engineers went further by building and testing a new kind of aircraft wing, assembled from hundreds of tiny identical pieces.
The new wing design, which can change shape and was covered with a thin layer of similar polymer material as the framework, was tested in a NASA wind tunnel.
“Because the structure, comprising thousands of tiny triangles of matchstick-like struts, is composed mostly of empty space, it forms a mechanical “metamaterial” that combines the structural stiffness of a rubber-like polymer and the extreme lightness and low density of an aerogel,” an MIT spokesperson said.
While the new wing was hand-assembled by a team of graduate students, the repetitive process is designed to be easily accomplished by a swarm of small, simple autonomous assembly robots.
“The research shows promise for reducing cost and increasing the performance for large, light weight, stiff structures,” said Daniel Campbell, a structures researcher at Aurora Flight Sciences, a Boeing company, who was not involved in the research. “Most promising near-term applications are structural applications for airships and space-based structures, such as antennas.”
Slimy eels
In 2014, scientists from Imperial College London (ICL) were studying slimy eels to find ways to improve aircraft performance that would lead to better fuel efficiency.
Working with the Toulouse Fluid Mechanics Institute and Laplace Labs, the scientists looked at how eels are able to ripple their skin as they move through the water.
“By carrying out simulations and experiments, the team were able to show that small-scale skin motions used by the eel reduces the friction between the skin and the water flowing over it, which helps it to move more easily through water,” a spokesperson from ICL said.
Researchers were able to mimic the skin-ripple quality in a new membrane-like material.
“Slimy eels may not be everyone’s cup of tea, but they are masters at manipulating their bodies to glide through their environment. Many aircraft components in existing planes have been inspired by animals and we are continuing to learn lessons from nature,” said Professor Jonathan Morrison, from the Department of Aeronautics at (ICL).
He added: “We are making many exciting advances in the field of aircraft design, which will mean quieter, cleaner and greener planes in the sky in the future.”